Overseas Game Manufacturing Demystified (or How to Avoid a Disaster)
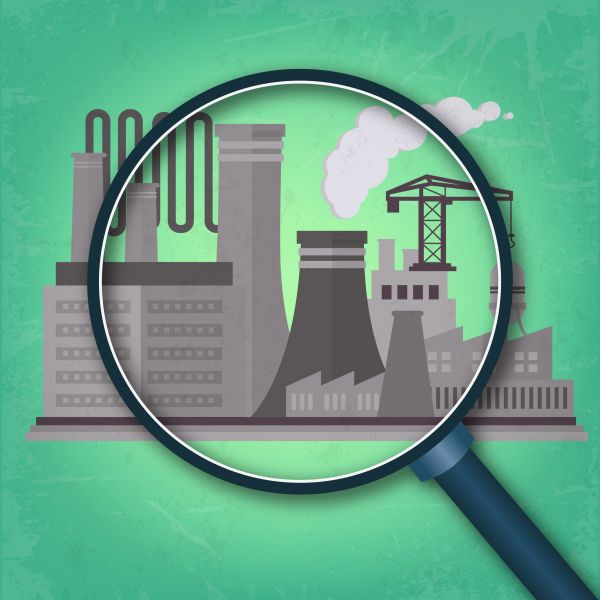
So you've been working on a game idea for years — writing and rewriting rules, sweating over just the right theme, working endlessly on the graphic design, scrounging components from other games, cutting and taping and cobbling together pieces and parts, and then playtesting with family and friends over and over and over again. You finally get it to the point where you think it can become a real, live product. Out there in the marketplace, for the whole world to buy. The ultimate proving ground. You've been hearing enough positive feedback from everyone around you that you really do believe it: this game could actually become a commercial success.
So you take the project to the next step. Along with a whole bunch of money, you send your blood, sweat, and tears to some factory on the other side of the world, and simply cross your fingers that what you'll finally receive will even approximate what you wanted for a finished product. The quality will be far less than what you hoped for, it will take about twice as long to produce as you thought it would, and you'll have to pay more money than you thought you would for expenses that you never anticipated. Sounds like a scenario you might expect, huh? Wrong.
Manufacturing your game overseas does not mean you must compromise on quality. It doesn't mean that your budget will be blown, and doesn't mean that you'll be at the mercy of haphazard production scheduling fraught with unexplainable delays. All those terrible situations are not a function of geography. You can experience them all with a factory right in your own back yard. The problems often are a function of a lack of knowledge of who you are working with, what their capabilities are, a disconnect in expectations, and a lack of communication. Ensuring that your manufacturing experience is a positive one boils down to just a few key elements: properly vetting your manufacturing partner, proper planning throughout the entire process, and lots and lots of communication.
For all practical purposes, in our industry, overseas manufacturing means manufacturing in Mainland China. Why? It's all about costs. Access to lower cost labor, facilities, and materials make China the obvious choice. Of course, a simple review of consumer products in other industries will yield a plethora of countries where manufacturing takes place. Other countries around the world may offer lower cost labor, or cheaper material sourcing, but the critical issue that still makes China the obvious choice for game manufacturing is stability. Stability for game manufacturing is defined by access to and consistency with the wide variety of materials that are typically used in games, safety compliance with those materials (now mandated for children's products sold in markets around the world), adherence to workplace safety and employee practices as defined by both the International Council of Toy Industries (ICTI) as well as some major retailers, and finally stability with pricing and production capacity.