Overseas Game Manufacturing Demystified (or How to Avoid a Disaster): Page 3 of 4
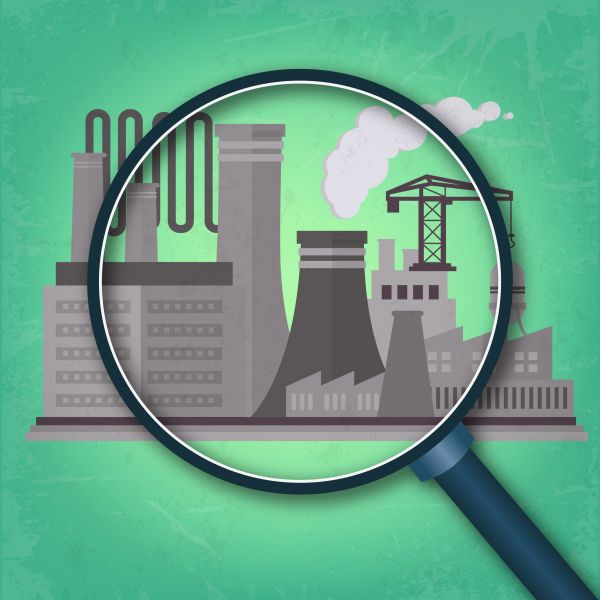
The second key element is planning. Planning is the lifeblood of a successful game development and manufacturing process. You've put a huge amount of planning into the development of your game play and determining the target market for buying the game. The next step is the planning of the physical elements of the game. This is where the product specifications that define your game come in. This includes the materials, the assembly, even the type of shipping carton that your games will be packed in. Planning includes the product safety testing that your game will be subject to. And planning also includes mapping out the entire project timeframe — the graphic design, preparation of press plates for printing and development of molds for plastic components, approvals of preproduction samples, the actual manufacturing, and finally the freight forwarding of the goods to your final destination.
The third key element in a successful game manufacturing project is communication. There just can't be enough of it. Obviously, there are many steps involved in the process. Communications needs to be taking place throughout. There really shouldn't be any points in time where you find yourself saying "I haven't heard from my project manager in a long time", or (worse!), "deadlines are slipping and I don't know why." The manufacturing process needs to develop and maintain momentum, meaning that each step along the way is the accomplishment of a task. If you're not sure where you are in that process, what the next step is, or when the next deadline will be reached, then at the very least you're not getting the communication you need to make the process flow successfully. You need to be receiving regular updates — when you'll be receiving preproduction samples, when new press proofs will be submitted, when the molds samples will be completed, when the assembly will start and finish, when the safety testing report will be issued, when the goods will be delivered to the overseas port, and when they are due to arrive at your warehouse.
So, you've figured out what components will constitute your game, and you're underway with your graphic design. The project specifications need to be developed with your project manager. These specifications include a vast number of details about the project — everything needed to be able to properly determine the cost to produce, but also the roadmap for the factory to properly manufacture the game. Examples would include dimensions for all components, the paper stock for the retail box, cards, rules, game board, etc. Paper stock in China is measured in grams per square meter (gsm), and is available in a wide range of thicknesses, qualities, and characteristics. Plastic components need to be documented in detail as well. There are many types of plastics available for molding: PVC, HIPS (high impact polystyrene), PP, ABS, and the list goes on. Good project specifications also identify how the components will be inserted into the retail box.
After detailed project specifications are developed, the manufacturing cost is determined, and the project begins. Dieline templates are created that your graphic designer will use to format the artwork to the dimensions of each component. Press plates are then created to produce preproduction samples of the printed materials. Molds are created for the plastic components (usually from detailed drawings, handmade sculptures, or 3D-printed prototypes). Samples of each component should be provided to you for approval before the final production is completed. After the manufacturing is done, and before the goods are delivered to the overseas freight forwarder, another sample should be sent to you for approval. Also, product safety testing needs to commence. This is a very detailed and (potentially) complex area, but as is the case with most every other step in the process, communication is key. The age grading of your game and the markets where the game will be sold are the two factors that determine exactly what tests need to be conducted. Countries around the world have differing testing standards, and if your game is designed for younger children, you'll need to comply with standards that differ from a game that is designed for older children or adults. The value of the project manager you're working with is important here — you need someone who is well versed on those standards, because this can affect the materials (or design of some components) that are used in the project. Also, make sure that you ask for a copy of the safety testing report — it will be issued by the testing lab that is contracted with to test the product. In the United States, the Consumer Product Safety Improvement Act (CPSIA), administered by the Consumer Product Safety Commission (CPSC) requires that this test be made available to the consuming public.